The digital twin is a virtual representation of real world assets and processes synchronized with sensors over the internet in fidelity. Thanks to this technology, physical objects can be controlled in real time by moving to digital environments. The technology behind digital twins has expanded to include large items such as machines, buildings, factories, and even cities, and with the advent of the metaverse these days, it has further expanded the concept by saying that even people can have digital twins. The idea first originated at NASA, and within a few years of Gartner naming the term “digital twin” as one of the top 10 strategic technology trends of the next 10 years, it has soon become a data provider for more than 20 billion IoT/OT connected sensor or endpoint digital twin products today. Thanks to this use situation, today half of the large industrial companies, mainly in the field of production life cycle (PLM), use digital twins, and these organizations have achieved an average improvement in product efficiency of 10%.
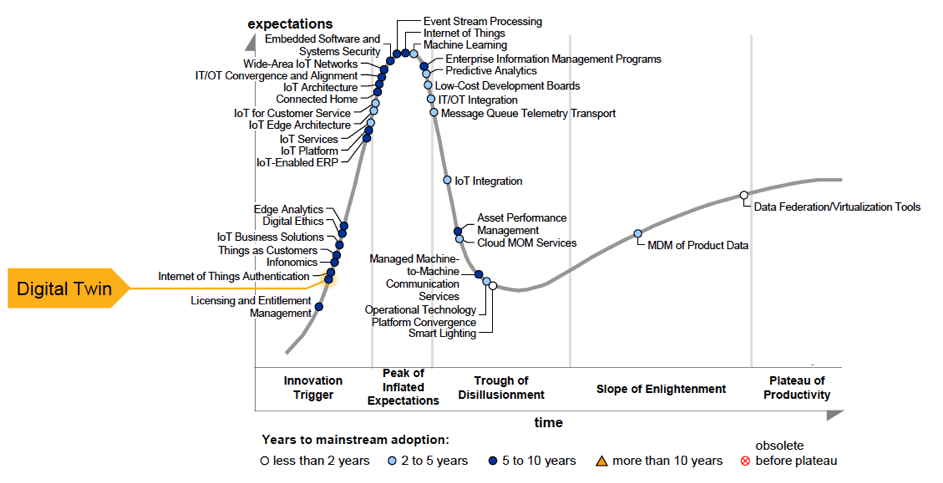
What Are the Benefits of Digital Twin Technology?
As a result of the acquisition of the Internet of Things and digital twin technologies with the transformation of industry 4.0, enterprises have made many gains on the part of the business unit. If we consider the main benefits;
· Risk Management and Production Efficiency;
Thanks to the digital twin, companies can test and verify a product before it exists in the real world. The digital twin creates a copy of the planned production process, allowing engineers to identify all process errors before the product goes into production. Engineers can disrupt the system to analyze unexpected scenarios, study the system's response, and determine corresponding mitigation strategies. This new capability improves risk assessment, accelerates the development of new products and increases the reliability of the production line.
· Maintenance Forecasting and Optimization;
Because it creates big data in real time with sensor data provided in digital twin systems, businesses can analyze their data to identify problems in the system in advance. This capability enables enterprises to more accurately plan upstream maintenance actions, increasing production line efficiency and reducing maintenance costs.
· Real-Time and Centralized Monitoring;
It is often very difficult and complex to obtain a real-time, detailed view of corporate systems that are spread over large and wide geographies. However, with a digital twin application, it is quite easy to create and manage systems that are accessible from anywhere, providing these institutions with the ability to remotely monitor, control, and intervene instantly on system performance.
· Easy Automation and Collaboration;
24/7 access to data such as system information and process automation improves performance and efficiency, enabling greater focus on interteam collaboration in maintenance and production processes.
· Finance;
Thanks to the digital twin, the ability to integrate OT-based data such as raw material and labor costs with traditional IT-based financial data can be acquired quite easily. Thanks to the analytical processes of large amounts of real-time data, it allows enterprises to make better and faster decisions about whether activities in a production chain are financially viable or not.
With digital twin technology, numerous applications have been introduced in these sectors and connected business lines, and many are waiting to discover its potential to mature and develop.
Production Processes: Digital twin is considered the key technology under the heading of industry 4.0 to realize comprehensive digital description of components, products and systems, including information from all stages of the product lifecycle. The Product Lifecycle Management (PLM) strategy has been present in the industry for many years and is considered the most effective way to manage a company's components, products and systems across all life cycles, from the initial idea of the product to the product idea, and the term digital twin also addresses the issue of PLM with industry 4.0 with a powerful end-to-end approach.
Automotive Industry: In the automotive industry, a huge amount of data is generated at every stage of the product life cycle of vehicles. Such big data makes it possible to create faster, cost-effective and high-quality products. Still, automotive manufacturers have different levels of data efficient use, and it is estimated that companies analyze only 12% of the available data. https://research.aimultiple.com/big-data-stats/#business-big-data-adoption Suppose an international automotive company that manufactures every stage of vehicles around the world. To create the digital twin of the vehicle, data management capabilities in different regions involved in the product lifecycle must be competent and high-level. It is expected that an ideal automotive industry stakeholder who has achieved the transformation of Industry 4.0 will be able to reveal the relationships of all IT/OT data provided in the PLM stream below and make numerous predictive estimates from this data together with the digital twin. https://www.smmt.co.uk/2018/12/role-of-digital-twin-in-automotive-industry
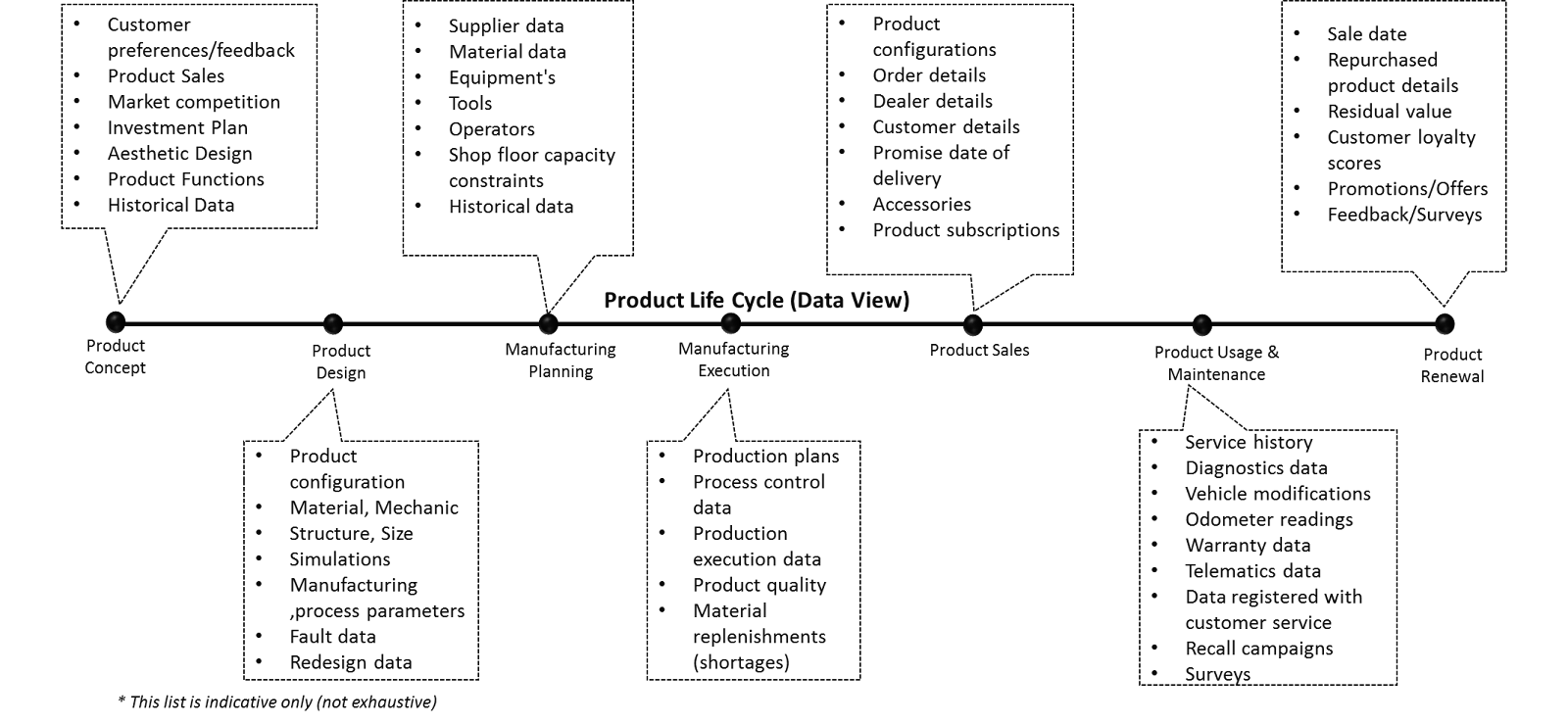
Health Sector: Digital twin technology can also be used to model the genome structure, physiological characteristics and lifestyle of an individual to create personalized medicine. It typically has a more individual focus than precision medicine, which focuses on sample groups within the population. Developing the Digital Twin of a human body consists of a more advanced process than any engineering product. Sensor devices can efficiently provide data to the Digital Twin of any designed object. Especially with Covid-19, the development of digital twin scenarios in various fields of activity in the health sector has gained momentum. https://www.cbinsights.com/research/digital-twins-technology-healthcare
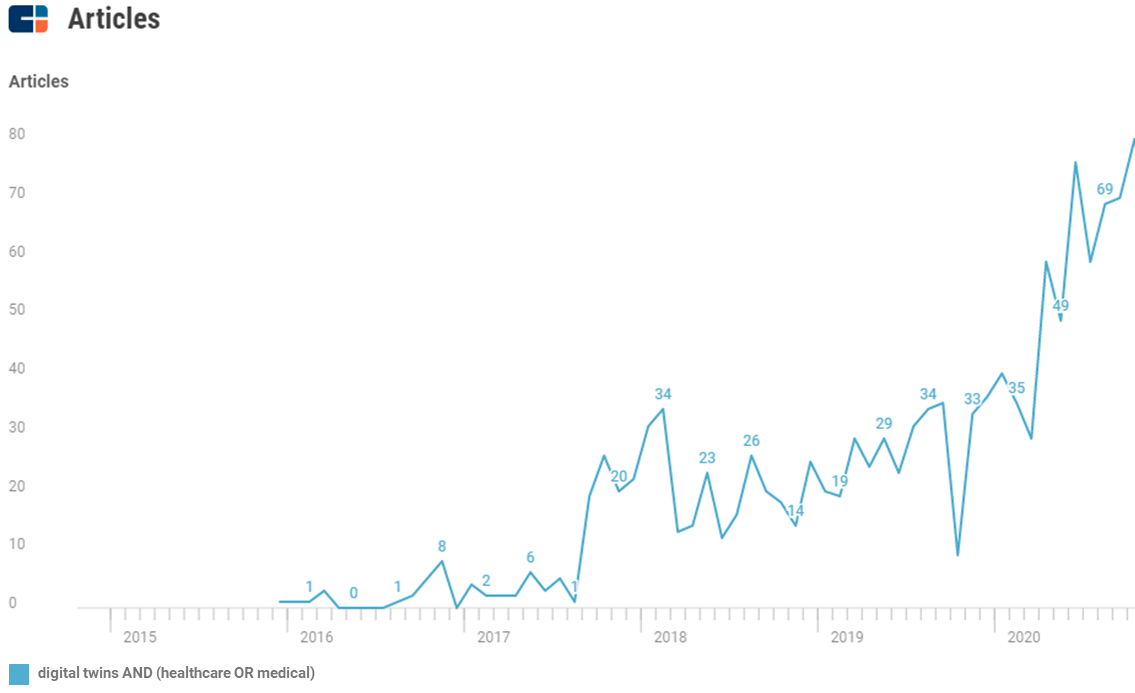
Smart City Applications: The use of digital twins, which can display 3D and 4D spatial data in real time and also incorporate them into environments such as augmented reality or the metaverse, will significantly help civil engineers and others involved in urban planning activities.
1. Infrastructure Planning: Builds competence for lighting systems, 5G, Wi-Fi, video surveillance and more.
2. Indoor Airflow Simulation - Supports optimized interior designs to minimize the spread of COVID-19.
3. Emergency Response — Provides a real-time view of city assets and resources against possible natural disasters.
4. Open spaces & Marketplaces: Enables the integration of the public data ecosystem as a third party and maximizes public-citizen interaction.
5. Green Conversion: Provides data-specific control over factors such as vehicle impact and water, including simulation of the impact of factors such as air and noise pollution, CO2 emission, carbon footprint on green conversion.
6. Sustainability: Helps support the most efficient production and use of renewable energy and recycling optimization.
By 2025, digital twins will be deployed to more than 500 cities worldwide. That is why it is necessary for the authorities in this area to start the necessary work to create digital copies of all cities and their systems. https://www.abiresearch.com
As Komtaş Knowledge Management, our approach is to treat digital twin processes as a data-driven operational resource for the design and production of products. The Digital Twin should be well analyzed according to technical and business hierarchies, and structured in accordance with the workflow culture of the organization. The product, which is in the focus of industrial service, consists on the one hand of sub-components, and on the other is part of a larger system. For this reason, in IoT systems, objects can vary with different components, from physical components to integrated machines, workshops, factories and factory systems. All components are parts of a whole for us.
In the industrial world, it requires framing the B2B (business-to-business) environment and complex application areas of digital twin applications in a context of sustainable and maximum efficiency with a data-driven digital twin lifecycle. The fundamental question most asked by institutions around this framework is:
“In a complex data-driven product service system, what service value can a digital twin provide? Who is the provider? Who is the beneficiary and with what data are analytical techniques necessary?”
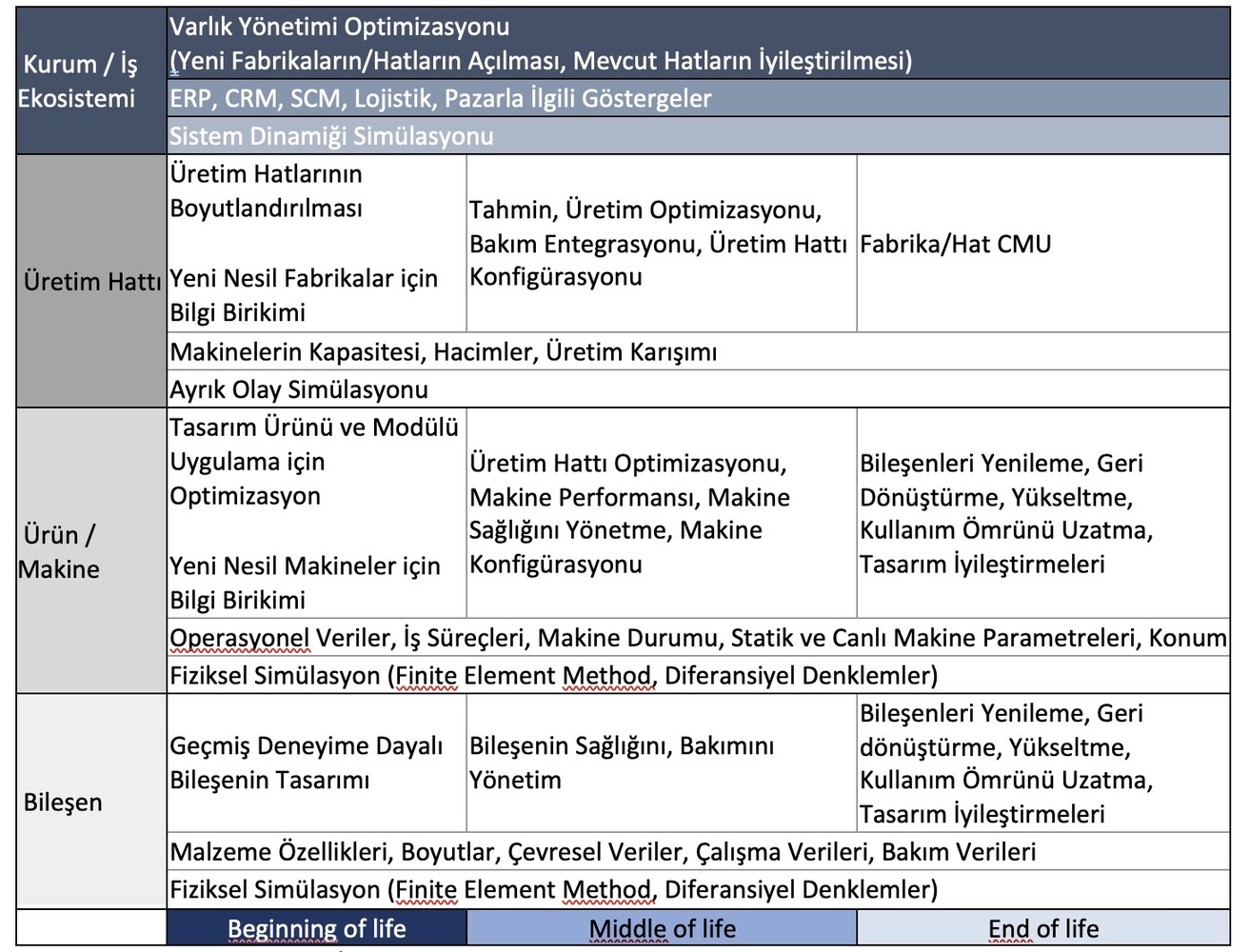
As Komtaş, we are ready to answer all your questions together with our data-driven digital twin approach and global solution proposals.
İlginizi Çekebilecek Diğer İçeriklerimiz
Bu yazıda Informatica World 2025'te duyurulan yeniliklere, IDMC platformunun yol haritasına ve önümüzdeki döneme dair Informatica’nın stratejik yönelimlerine değineceğiz.
At the Google Cloud Next '25, many innovations were announced in the field of artificial intelligence and cloud that will closely interest developers and decision-makers. In this article, we compile and summarize the main topics introduced at the event.